Master Theses
Arches Lab provides an active learning and highly collaborative and interactive environment for Master of Science students to gain hands-on experiences in design and development of heterogeneous architected materials.
Different topics with combinations of analytical, numerical and experimental approaches are available for master thesis proposals. The durations for developing a full Master thesis in our lab is generally 6-9 Months.
If interested in developing your thesis in our lab, please contact Prof. Bagherifard (sara.bagherifard@polimi.it) to schedule an appointment.
The low working temperature of cold spray technology offers a unique possibility to deposit a wide variety of composite materials by mixing two or more constituent powders. However, while it is possible to precisely control the chemical composition of the mixture before spraying, the compositional yield in the deposit remains uncertain.
The objective of this thesis is to develop numerical model of the deposition process to consider the effect of interparticle interaction, sequence and volume fraction in mixed feedstock on deformation and bonding state. Experimental cold spray wipe tests and Coating microstructural analysis.
Defect prediction and mitigation are a major subject in the field of Additive Manufacturing (AM). CS, as a meltless AM technique, results in the absence of solidification defects in the material’s microstructure. This characteristic makes it attractive for AM and repair purposed in several highly demanding aerospace and automotive applications. Porosity can be a major drawback in Cold Spray (CS) deposition, weakening the mechanical performance of sprayed parts. Your work will focus on analysing CS samples fabricated with different process parameters to understand their influence on porosity.
Shape control in cold spray coating and additive manufacturing is still a major challenge. Customized robot programming and predictive numerical tools are being extremely helpful; however, masking is also a simple and scalable technique for deposit shape control. In this project, masking and spray set-up designs will be analyzed to control the shape and thickness of the deposit and thus provide solutions for patterned surfaces. An alternative can be 3D printing of polymer moulds that can be later removed.
Heterostructured material have separate regions with dramatically different mechanical/physical properties. Severe plastic deformation-based techniques have been recognized as an efficient tool in generating microstructural heterogeneity in metallic materials.This work experimentally analyzes the effect of selective ultrasonic shot peening on mechanical response of steel specimens.
By controlling the design, shape and density of the patterns on treated/un-treated areas the global response of the material can be controlled to obtain customized mechanical performance.
Cold spray using sub-optimal parameters can induce specific porous features on the substrate and generate a unique morphology in the coating. The idea behind this project is to conduct a comprehensive literature review on porous iron coatings and cold spray technology to identify knowledge gaps and challenges. Then design experiments for depositing porous Fe coatings using cold spray, focusing on process parameters, followed by experimental characterize the microstructure, mechanical properties, and functional performance of the coatings using microscopy and mechanical testing methods.
Cold spray has great technological potential in the repair sector, thanks to its high material flexibility, lack of adverse effects on the underlying substrate, and retainment of the mechanical properties of the feedstock. Current limitations of the process include the lack of geometrical control of its deposits.
Developing advanced frameworks for defect contour identification and tailored planning of the tool trajectory during spraying would represent significant steps towards automating Cold Spray repair.
Possible approaches to the problem could include defect shape prediction and trajectory optimization aided by machine learning methods.
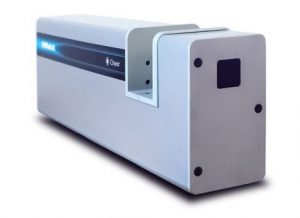
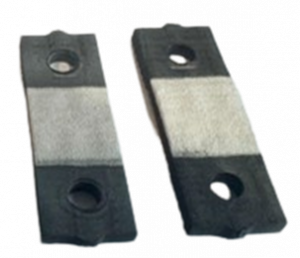
In CS ideally the nozzle velocity is held constant to maintain a uniform deposit. Taking turns always results in an acceleration ∴ a non-uniform deposit. To tackle this in CSAM there are a few different existing strategies. Reduce the speed &/or increase the turn radius. These focus on reducing the amount & duration of accelerations. Adding additional axis can also be used to combat the acceleration effects. In CS practice this is either done with a 2 rotational axis positioner or another 6-axis robot arm. Consumer FDM printers couldn’t afford the cost & complexity of an additional axis. To solve this, they looked at maintaining a constant rate of material deposition rather than nozzle speed (Pressure Advance).
The thesis aims to develop a monitoring system to capture powder behaviour during shutdowns. It will run tests with various powders and feed tube lengths to establish a correction similar to pressure advance or equivalents in WAAM and LMD to enhance shape control for complex-shaped components.